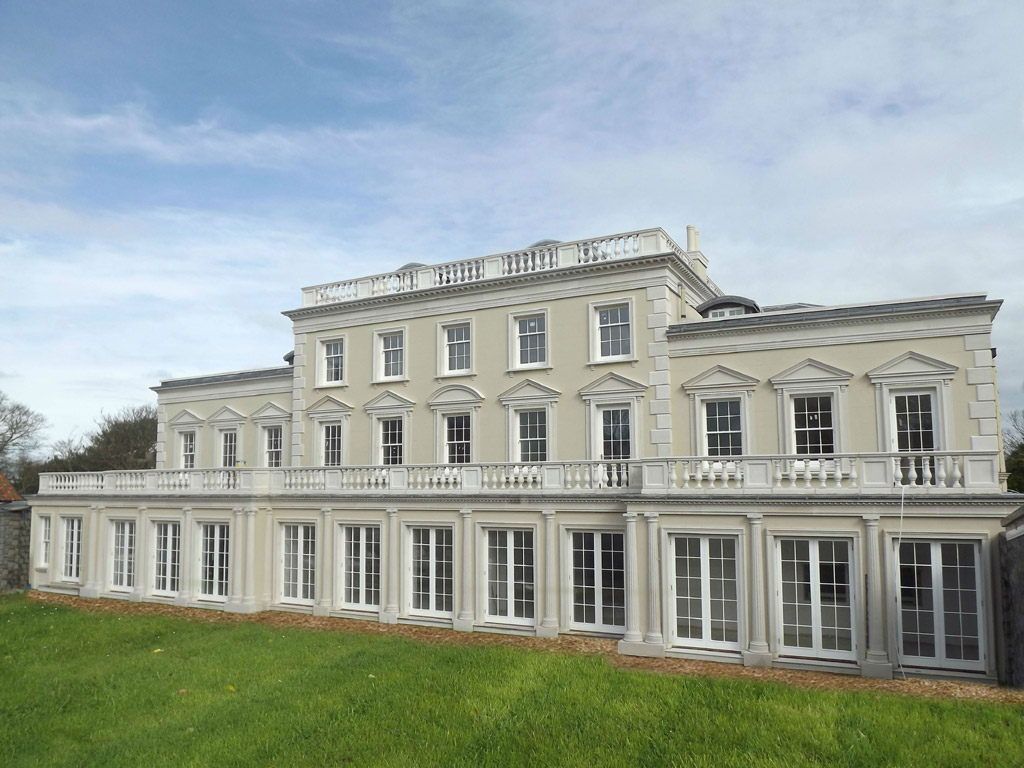
One of the most impressive private homes
In excess of 2,500 stone components were packed and shipped to Guernsey by UKCSA Full Member Pennine Stone Limited for the construction of one of the most impressive private homes to be completed on the Channel Islands in many years.
This property was built to the most exacting of standards. Design excellence was paramount; and Pennine Stone first began a dialogue with the property owner in 2012; initial project meetings commenced in 2014 but it wasn’t until 2016 that the first stones were shipped, with the final deliveries being made in 2017.
The client set out to construct an outstanding property; classical elevations, impressive footprint, yet designed to be a family home, albeit with added extras such as an integral ballroom. With a 350 mile delivery route incorporating road and sea, a comprehensive understanding of the build sequence was essential. Production and delivery schedules needed to be agreed months in advance of products being required on site.
Each product was bespoke and hundreds of moulds were needed – many moulds had to be stored for nearly 2 years in case additional or replacement items were required. There was to be no compromise on the quality of the materials used for this building; a challenge when the stone requirement for the property included 58 cast stone window surrounds and over 20 cast stone door surrounds. It was essential that the fitting teams were highly skilled, experienced and extremely professional and it was a godsend that the client had instructed an excellent installation team – UKCSA Associate Member PCS Stone Specialists.
A full understanding of the build sequence and excellent communications were required by Pennine Stone to make this project successful. It is a testament to the skill and focus of all those involved at Pennine Stone that, over the full length of the project, only 3 stones required replacement due to damage. The dentil string course was a particular challenge – this was not a project where standard lengths could be cut on site, due to restrictions and cast in fixings, so great care was needed by the production, packing and fitting teams in order to ensure that the right products could be identified and installed in the correct position in order to achieve the desired visual flow.
The design also demanded that a different dentil solution was required for each floor, so, unfortunately, there would be no sharing of moulds. The moulds for the fluted columns were especially complex bespoke rubber lined GRP and timber, to produce the fibre reinforced final units. The columns at the front of the building were the same design, but a different height to the columns at the rear, again requiring additional moulds – a further example of design excellence and a refusal to compromise on this project.
All the cast stone supplied to this project was fibre reinforced, which enabled the component weight to be minimised, but considerably added to the complexity of the mould design. The cast stone was supported and restrained by a stainless steel system designed by UKCSA Associate Member, PCS Stone Specialists , and manufactured and supplied by UKCSA Associate Member, GA Fixings Ltd, and installed by PCS themselves.
The finished home is a testament to the vision of the client, his design team and his suppliers – truly a “show stopper” building which would not have been possible without the full co-operation and co-ordination of all involved