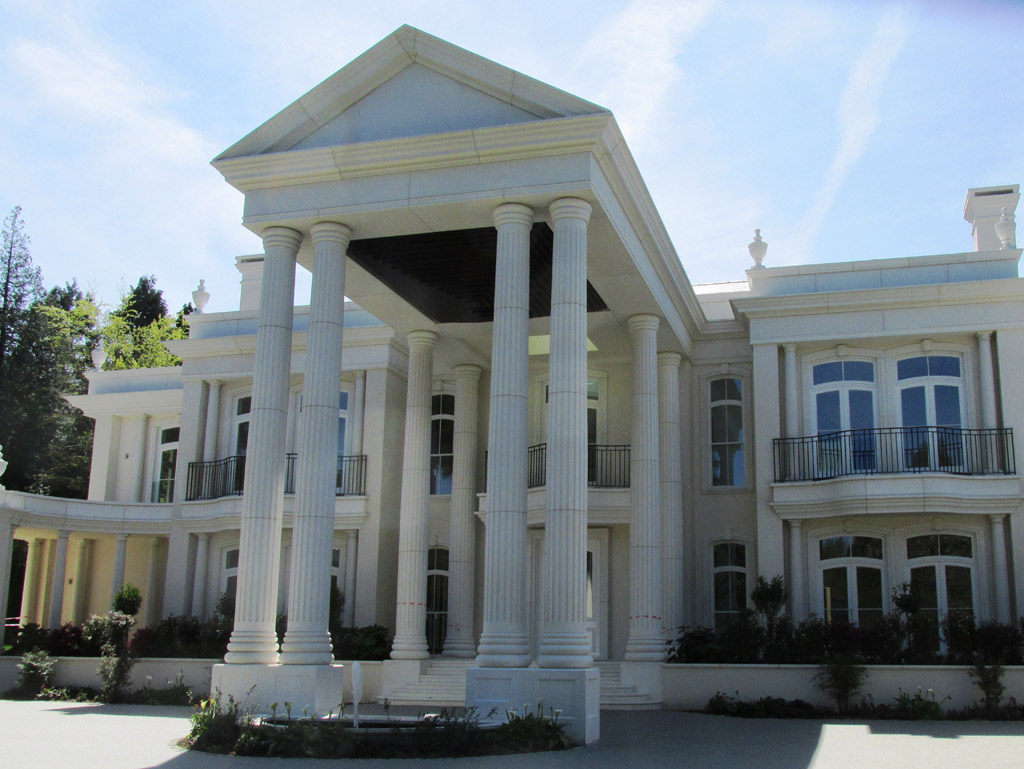
Positioned in a prime location on the exclusive and internationally renowned ‘St Georges Hill’ private estate near Weybridge, the 26,000ft2 Fosseways development, with cast stone from UKCSA Member Woodside Cast Stone, certainly makes a statement. The main feature on this private residence is a 12m high Porte Cochere assembly on the main entrance area with 8no. fluted columns, spanned with a bullnosed architrave beam, suspended soffit and a gable pediment assembly that projects 11m forward of the main building line that is hung from a steel frame.
Other than this main assembly, one particular component within the supply that took a lot of thought and consideration was a 6.7m long moulded cornice beam, cast in one piece and weighing in excess of 4.5t that was designed to carry the 20t building above.
The stone to the first floor sweeping and curved balconies form permanent shuttering and were installed at the very start of the main build process when the concrete frame was cast. A lot of care was taken by UKKCSA Member Woodside, the developer and installers to protect these features from damage during the build programme and the results of this diligence are clear to see. Other stone features include 66no. 3.5m high columns on the balconies as well as a 1.94m high entablature assembly at eaves level, topped with 20no. bespoke urn finials to add to the effect of grandeur.
As well of the main building that occupies three spacious floor levels there are two substantial detached buildings (one that is two–storey and the other that is three-storey) that house garages with six parking spaces and staff quarters. To give an idea of scale, these two, supplementary, detached buildings occupy 3,500ft2, which is the size of a typical, detached four bedroom house.
Large scale units were designed with the brief to minimise jointing visibility and a special wet-cast, etched, stone mix was designed by ourselves, containing Nordic Spa aggregates, to conform to the client’s wishes for the stone to be as white as possible. This is certainly achieved as when you drive past the development it catches your attention with the brightness and freshness of the stone.
Woodside’s Technical Department worked closely with the developer from the outset to ensure that the design brief was implemented, giving careful consideration to every step in the detailing, manufacturing, handling, storage and installation process to ensure a successful development completion. Units were delivered to meet the complex choreographed sequence of installation as any damage would have had a catastrophic effect on the build programme whilst a replacement unit was manufactured.